Injection Moulding Die Cost - The Key to Cost-Effective Manufacturing
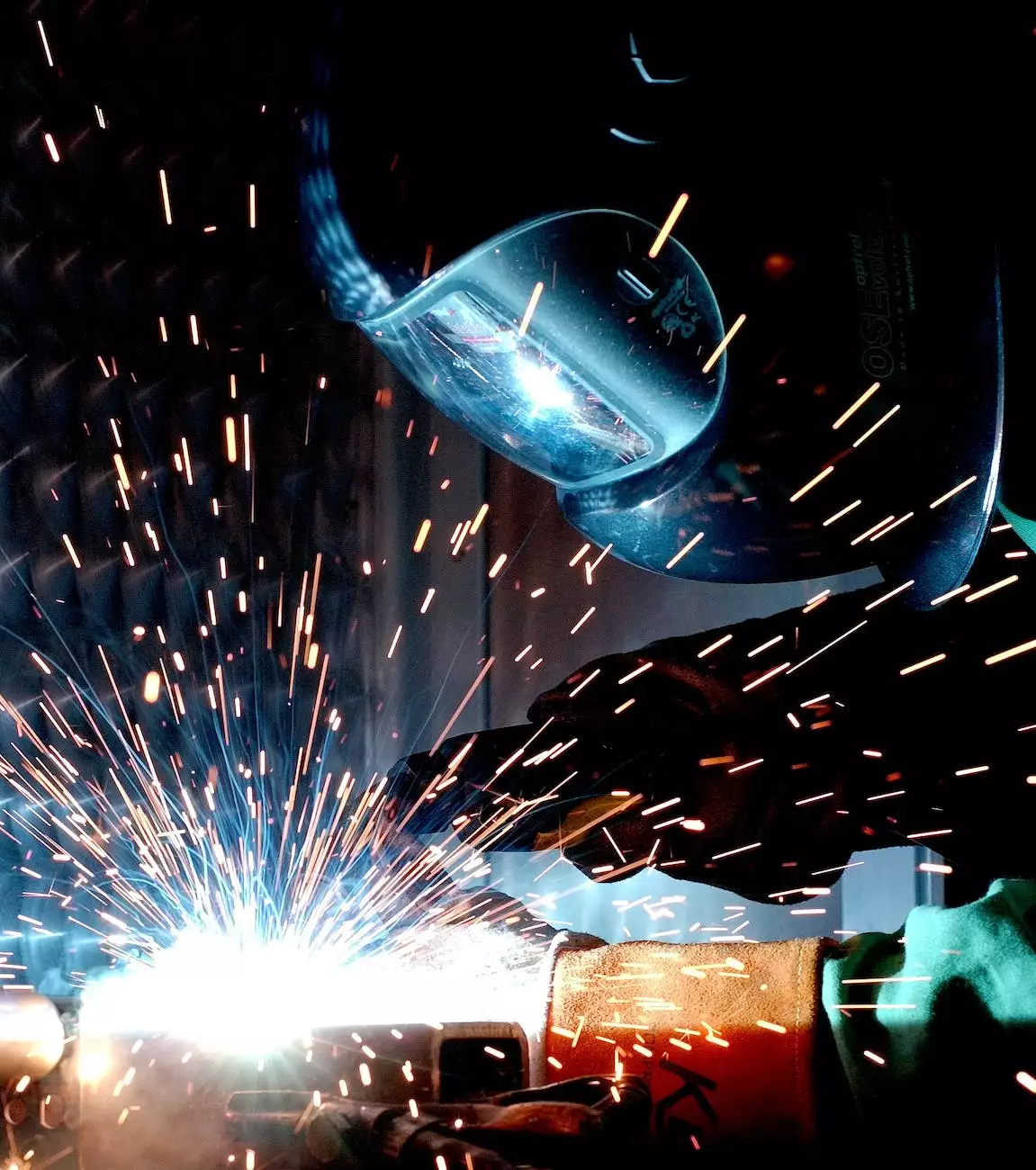
When it comes to cost-effective manufacturing in the 3D Printing industry, one crucial factor that businesses and manufacturers need to consider is the injection moulding die cost. Injection moulding plays a significant role in the production process, and optimizing the cost associated with moulding dies can result in substantial savings and improved profitability for businesses.
Understanding Injection Moulding Die Cost
Injection moulding dies, also known as moulds or tools, form the backbone of the injection moulding process. They are custom-made to create precise and complex plastic components with high accuracy and repeatability. However, the manufacturing and maintenance of these moulds come at a certain cost, which needs to be carefully evaluated and managed.
Several factors influence the overall cost of injection moulding dies, including:
- Mould Design Complexity: The complexity of the desired plastic component greatly impacts the mould design complexity. Complex designs require intricate moulds, which can significantly increase the overall cost.
- Mould Material: The type of material used to manufacture the mould plays a vital role in its cost. While steel is a popular choice due to its durability and longevity, it is more expensive compared to aluminum or other alternatives.
- Cavities and Cores: The number of cavities and cores required in the mould design affects the manufacturing cost. Increased cavitation requires more precise machining and can result in higher overall costs.
- Tolerance and Surface Finish: If the desired plastic component has strict tolerance and surface finish requirements, the mould needs to be manufactured with enhanced precision and attention to detail, which can impact the overall cost.
- Mould Size: The physical size of the moulded component influences the material required for the mould, the complexity of the machining process, and ultimately, the cost.
- Number of Shots: The number of shots, or cycles, the mould can produce without requiring maintenance or replacement affects the overall cost. Moulds made for high-volume production generally have higher costs.
- Tooling and Maintenance: Investing in high-quality tooling and regular maintenance can help extend the lifespan of the mould and minimize ongoing costs.
Minimizing Injection Moulding Die Cost
While injection moulding die cost is an inevitable expense, there are several strategies businesses can employ to minimize these costs and achieve cost-effective manufacturing:
Optimized Design
Collaborating with experienced 3D Printing engineers and designers can help optimize the design of the plastic component, ensuring that it meets functional requirements while minimizing complexity. Simplifying the design can help reduce material and machining costs associated with the mould.
Material Selection
Choosing the right material for the injection moulding die is crucial in balancing cost and durability. Working closely with materials experts can help identify suitable alternatives that meet the desired specifications while reducing costs.
Multicavity Moulds
Utilizing multicavity moulds allows for the production of multiple plastic components simultaneously, resulting in higher productivity and reduced manufacturing costs per component. However, it is essential to consider factors like part quality, cycle time, and increased tooling complexity when opting for multicavity moulds.
Efficient Production Planning
Implementing efficient production planning and scheduling techniques can help optimize the utilization of injection moulding dies. By minimizing downtime and ensuring continuous production, businesses can maximize the value derived from each mould, ultimately reducing the average cost per part.
Regular Maintenance and Quality Control
Incorporating regular maintenance and quality control practices is crucial in extending the lifespan of the injection moulding die. By proactively addressing issues like wear and tear, damage, or deterioration, businesses can minimize unexpected costs associated with mould repair or replacement.
Partnering with QuickParts for Cost-Effective Manufacturing
When it comes to achieving cost-effective manufacturing in the 3D Printing industry, QuickParts is your trusted partner. With years of expertise in injection moulding and a commitment to high-quality results, QuickParts provides comprehensive solutions to help businesses optimize their injection moulding die costs.
At QuickParts, we understand the unique challenges faced by businesses in the rapidly evolving manufacturing landscape. Our team of skilled professionals collaborates closely with clients to develop custom-tailored solutions that deliver exceptional results while minimizing costs.
From initial design consultation to the production of high-quality plastic components, QuickParts combines industry-leading technology with a customer-centric approach to ensure the highest level of customer satisfaction.
Why Choose QuickParts?
- Expertise: With years of experience in the 3D Printing industry, QuickParts possesses the knowledge and expertise to tackle even the most complex injection moulding challenges.
- State-of-the-Art Facilities: QuickParts leverages cutting-edge technology and state-of-the-art facilities to deliver superior results, optimize efficiency, and minimize costs.
- Custom Solutions: We understand that every business has unique requirements. QuickParts takes a personalized approach to develop tailored solutions that meet your specific needs.
- Reliability: QuickParts prides itself on timely delivery and consistent quality. We prioritize customer satisfaction and strive to exceed expectations with every project.
- Cost-Effectiveness: By optimizing injection moulding die costs and employing efficient manufacturing processes, QuickParts helps businesses achieve cost-effective solutions without compromising on quality.
The Path to Cost-Effective Manufacturing
Optimizing injection moulding die costs is a vital step towards achieving cost-effective manufacturing in the 3D Printing industry. By considering factors such as mould design complexity, material selection, and maintenance practices, businesses can effectively manage and minimize these costs.
Partnering with QuickParts further enhances the journey towards cost-effective manufacturing. With our expertise, state-of-the-art facilities, and commitment to customized solutions, we can help you unlock new possibilities while maintaining a competitive edge in the industry.
Take the first step towards cost-effective manufacturing today. Contact QuickParts to discuss your injection moulding die needs and explore the possibilities of optimizing costs while delivering superior results.