Understanding the Role of Die Cast Mold Manufacturers in Metal Fabrication
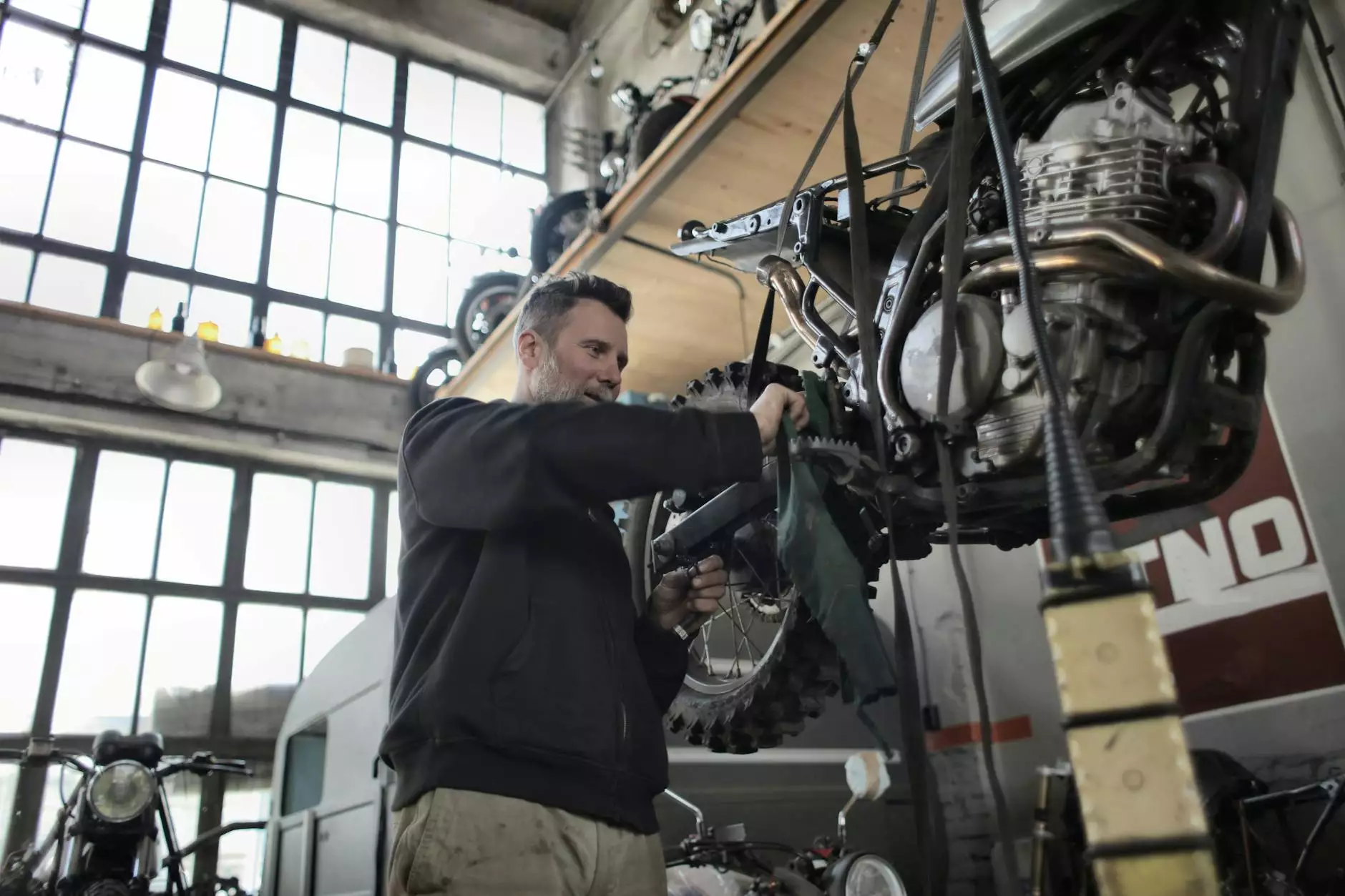
The manufacturing landscape today is continuously evolving, with die cast mold manufacturers playing a vital role in the metal fabrication industry. As various industries seek precision, durability, and efficiency, the demand for high-quality die cast molds is ever-increasing. In this article, we will delve into the nuances of die casting, the importance of selecting the right manufacturer, and how companies like Deep Mould can provide unmatched quality in production.
What is Die Casting?
Die casting is a manufacturing process characterized by forcing molten metal into a mold cavity under high pressure. This technique is popular due to its ability to produce parts with intricate shapes and fine surface details. The process is often used for metals with a melting point under 450°C, such as aluminum, zinc, and magnesium, making it a preferred choice in various applications.
The Benefits of Die Casting
Die casting provides numerous advantages that make it an attractive option for manufacturers:
- High Precision: Die casting offers exceptional accuracy and repeatability, producing parts that are often finished without the need for further machining.
- Complex Geometries: The process allows for the creation of intricate shapes that would be impossible or very costly to achieve through other methods.
- Improved Surface Finish: With die casting, the products typically have a smoother finish, which reduces post-processing work.
- Efficiency: High production rates and minimal waste make die casting an efficient manufacturing method.
- Cost-Effective: For high-volume production runs, die casting is economical, reducing material usage and manpower costs.
The Importance of Die Cast Mold Manufacturers
Finding the right die cast mold manufacturers is critical to achieving quality results. Key factors to consider when selecting a manufacturer include:
1. Experience and Expertise
Experience plays a vital role in the die casting industry. A manufacturer with a proven track record in die casting understands the complexities of the process and can navigate challenges effectively. They should have a portfolio demonstrating their capabilities and experience across various industries.
2. Technological Advancements
In today's fast-paced manufacturing world, keeping up with technology is crucial. Leading die cast mold manufacturers invest in the latest equipment and software, ensuring they can provide superior service and quality. Techniques such as simulation software can help predict potential issues, leading to improved mold performance and longevity.
3. Quality Assurance Processes
A reliable manufacturer implements stringent quality assurance processes. This includes regular inspections, testing of the dies, and adherence to international standards. A commitment to quality will minimize defects and ensure consistency throughout the production process.
Choosing the Right Die Cast Mold Manufacturer
When looking for the ideal die cast mold manufacturer, companies should assess the following key aspects:
1. Customization Capabilities
The best manufacturers offer customization options to meet specific project requirements. Whether you need a small batch or large-scale production, the ability to tailor the design and functionality of molds is crucial for achieving desired results.
2. Material Options
Different projects may require different materials for die casting. Leading manufacturers provide a broad range of metal options, including aluminum, zinc, and magnesium, to optimize the performance of the end product.
3. Production Capacity
The capacity to meet production deadlines without sacrificing quality is essential. A manufacturer’s ability to scale operations according to demand is an important consideration for businesses looking to maintain a steady supply chain.
4. Customer Support
Exceptional customer service is a hallmark of a reputable die cast mold manufacturer. From the initial consultation through to after-sales support, effective communication and responsiveness can enhance the overall manufacturing experience.
Innovations in Die Casting Technology
The die casting industry is continuously innovating, leading to improved processes and products. Some noteworthy advancements include:
1. 3D Printing for Mold Creation
Utilizing 3D printing technology allows manufacturers to create molds faster and more efficiently. This change can significantly reduce lead times and allow for more reliable prototyping, ultimately leading to quicker go-to-market strategies.
2. Enhanced Materials
Research and developments in new alloys have produced stronger and lighter materials tailored for die casting applications. These materials can withstand higher temperatures and pressures, improving the performance of cast products.
3. Smart Manufacturing
The integration of IoT technologies and smart manufacturing solutions enhances data collection and machine monitoring. This advancement leads to improved operational efficiency and can help prevent costly downtimes.
Collaboration with Leading Die Cast Mold Manufacturers
Forming a partnership with experienced die cast mold manufacturers, like Deep Mould, offers several strategic benefits:
- Expert Guidance: Leverage the expertise of seasoned professionals during the design and prototyping stages.
- Quality Materials: Access to a range of high-quality materials that suit your specific requirements.
- Flexible Solutions: Collaboration allows for the engineering of flexible solutions that can adapt to changing market demands.
- After-Sales Support: Benefit from ongoing support, ensuring that any issues post-production can be addressed swiftly.
Conclusion: The Future of Die Casting
As industries continue to evolve, the role of die cast mold manufacturers becomes more crucial than ever. The ability to produce high-quality parts with precision and efficiency sets the foundation for many emerging technologies. By choosing a reputable partner like Deep Mould, companies can ensure they remain competitive in this ever-changing landscape.
With a focus on quality, innovation, and customer satisfaction, the future of die casting looks promising. Embrace the advantages offered by expert manufacturers and experience the benefits of efficient and reliable metal fabrication.