Comprehensive Guide to High Pressure Die Casting Mold: Unlocking Excellence in Metal Fabrication
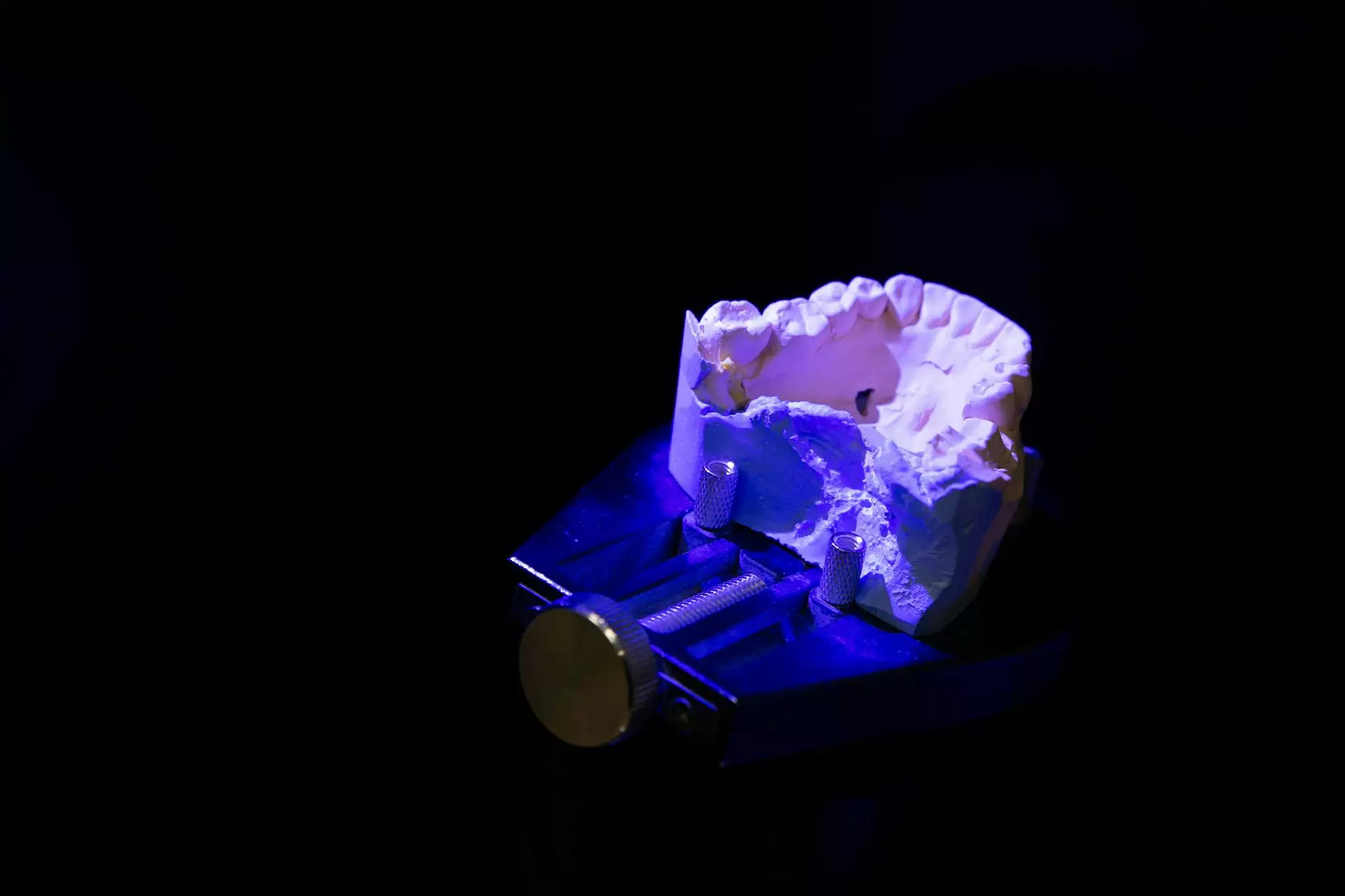
In the dynamic world of metal fabrication, achieving precision, efficiency, and cost-effectiveness is paramount. Among the various manufacturing processes, high pressure die casting mold stands out as a transformative technology, enabling the production of complex metal components with unparalleled accuracy and superior surface finishes. At deepmould.net, we understand the critical role that custom high pressure die casting molds play in elevating manufacturing standards and driving industrial innovation.
Understanding the Power of High Pressure Die Casting Mold in Modern Manufacturing
The high pressure die casting process involves injecting molten metal into a precisely crafted steel mold under significant pressure. This method is renowned for its ability to produce intricate shapes, high-volume outputs, and consistent quality, making it invaluable across industries such as automotive, aerospace, electronics, and consumer goods.
What is a High Pressure Die Casting Mold?
A high pressure die casting mold, also known as a die or tooling, is a specialized metal cavity designed meticulously to shape molten metal into specific components. The mold comprises two main halves—die core and die cavity—which form the internal and external contours of the manufactured part. Precision engineering, high-grade materials, and advanced cooling systems are integrated into the mold to ensure durability, accuracy, and repeatability.
The Significance of High Pressure Die Casting Mold in Metal Fabrication
The significance of a high pressure die casting mold in the realm of metal fabrication cannot be overstated. It serves as the backbone for mass production of high-quality components and offers numerous advantages:
- High Production Efficiency: Capable of producing thousands of identical parts rapidly, thereby reducing manufacturing costs.
- Superior Surface Finish: Achieves smooth and detailed surfaces with minimal finishing required.
- Complex Geometry Capabilities: Facilitates the creation of intricate designs and precise tolerances impossible with traditional methods.
- Material Versatility: Compatible with various metals such as aluminum, zinc, magnesium, and copper alloys.
- Reduced Waste and Material Costs: Precise casting minimizes material wastage during production.
Design and Manufacturing of High Pressure Die Casting Molds: Best Practices
The effectiveness of the entire die casting process hinges significantly on the design and manufacturing quality of the high pressure die casting mold. Here are critical aspects and best practices to consider:
1. Material Selection for Mold Construction
The durability and longevity of a high pressure die casting mold depend heavily on choosing the right materials. High-grade alloy steels such as H13, P20, and S7 are often used due to their excellent toughness, thermal fatigue resistance, and machinability. Surface treatments like nitriding or carburizing can further enhance wear resistance and reduce corrosion.
2. Precise Mold Design for Complex Geometries
Advanced CAD software enables meticulous design of the mold's internal features, cooling channels, ejector pin placements, and gating systems. Properly engineered parts facilitate smooth molten metal flow, minimize defects like air entrapment or warping, and ensure ease of part ejection.
3. Incorporating Efficient Cooling Systems
Cooling channels are critical in controlling the solidification rate and reducing cycle times. Optimized cooling designs help achieve uniform temperature distribution, prevent thermal distortion, and enhance mold lifespan.
4. Precision Machining and Surface Finishing
High-tolerance machining processes such as CNC milling and EDM are essential to create detailed die features. Surface finishing techniques like polishing or coating reduce friction during ejecting and improve lifespan.
5. Rigorous Testing and Validation
Prototyping, mold flow analysis, and trial runs allow manufacturers to identify potential issues early, optimize design parameters, and validate mold performance before large-scale production.
Advantages of Working with a Premium High Pressure Die Casting Mold Supplier like DeepMould
Partnering with experienced manufacturers such as deepmould.net ensures access to high-quality high pressure die casting molds that meet stringent industry standards. Our specialization in the Metal Fabricators category guarantees:
- Customized Solutions: Tailored mold designs to meet specific project requirements and complex geometries.
- State-of-the-Art Technology: Cutting-edge manufacturing facilities and equipment for precision mold fabrication.
- Quality Assurance: Rigorous quality control processes, including nondestructive testing and inspections.
- Fast Turnaround: Efficient production workflows to minimize lead times without compromising quality.
- Technical Expertise: Experienced engineers and designers who optimize mold design for longevity and performance.
Key Industries Benefiting from High Pressure Die Casting Molds
The versatility and advantages of high pressure die casting molds extend across diverse sectors:
Automotive Industry
Fabrication of engine blocks, transmission cases, and interior components that require lightweight yet robust parts.
Aerospace
Manufacturing of complex structural components that must adhere to strict weight and strength specifications.
Electronics and Consumer Goods
Production of intricate housings, connectors, and electronic enclosures with high precision and smooth surfaces.
Medical Devices
Creating durable, high-precision components for medical equipment and instruments.
Future Trends and Innovations in High Pressure Die Casting Molds
The industry is continuously evolving with technological advancements that enhance mold functionality:
- Automation and Robotics: Integration of automated systems for mold handling and casting operations.
- Smart Mold Technologies: Use of sensors and IoT for real-time monitoring, predictive maintenance, and performance optimization.
- Advanced Materials: Development of new mold materials offering superior thermal management and wear resistance.
- Sustainable Practices: Eco-friendly manufacturing processes and recyclable mold components reducing environmental impact.
Why Choose DeepMould.net for Your High Pressure Die Casting Mold Needs?
At deepmould.net, our core mission is to provide premium high pressure die casting molds and related services that boost manufacturing efficiency, quality, and innovation.
- Technical Excellence: Our engineers utilize the latest design tools and manufacturing techniques to deliver molds that exceed expectations.
- Comprehensive Service: From initial concept and design to prototyping, production, and post-production support.
- Competitive Pricing: High-quality standards combined with cost-effective solutions ensure maximum value for clients.
- Global Reach: Serving clients worldwide with flexible logistics and customer-centric approaches.
- Industry Experience: Over a decade of expertise in die casting mold manufacturing for various industrial sectors.
Conclusion: Elevate Your Manufacturing with High Pressure Die Casting Mold
Investing in a high pressure die casting mold from a reputable supplier like deepmould.net sets the foundation for manufacturing excellence. Its role in producing high-precision, durable, and complex metal components makes it indispensable in today's competitive industrial landscape. Whether you are in aerospace, automotive, electronics, or other high-demand fields, harnessing the power of advanced die casting molds accelerates innovation, reduces costs, and ensures product superiority.
As the industry advances, continuous improvements in mold technology and design processes will unlock new possibilities for manufacturers. Partnering with experienced, innovative, and customer-focused experts ensures you stay ahead in this highly competitive market.